- お客様のニーズに合う製品を目指すこと (寸法・重量・搬入・据付方法含む)率先して提案を行うこと
- 安全性
- 使用性
- 点検性(停電作業)・締付点検を少なくするシンプル設計
- 施工性
- 清掃性
- 地震等の自然災害に強い製品
- 指定コスト内で如何に良い製品を作るか努力すること
- 重要な製品である。社内作業も工夫して安心出来る製品を確立すること
- 出荷は、検査部長以上、幹部が製品を全確認しなければ許可できない
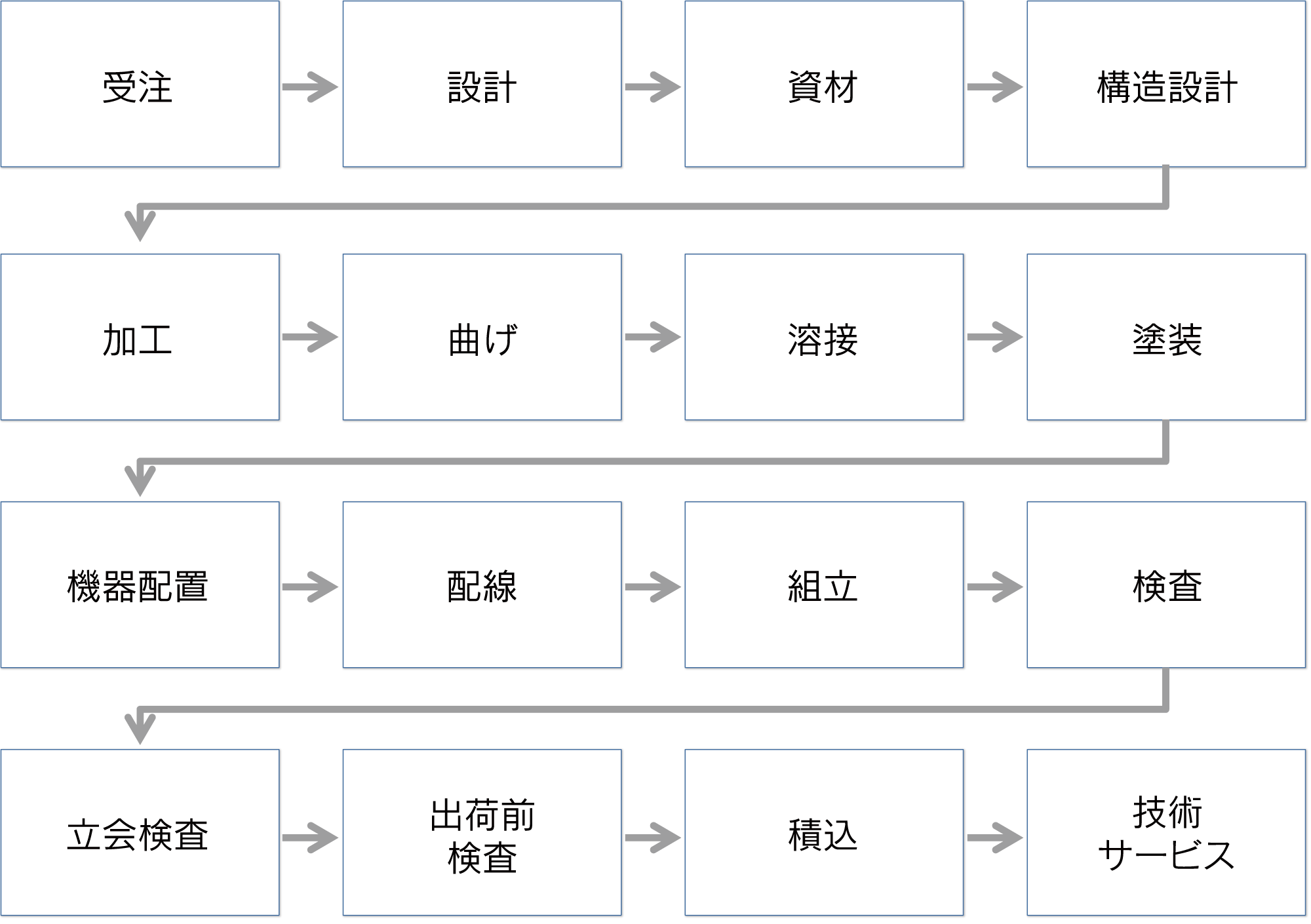
※製造期間は、図面承認後2ヶ月と致します (目安)
※立会検査から出荷までは、是正期間として1、2週間と致します (目安)
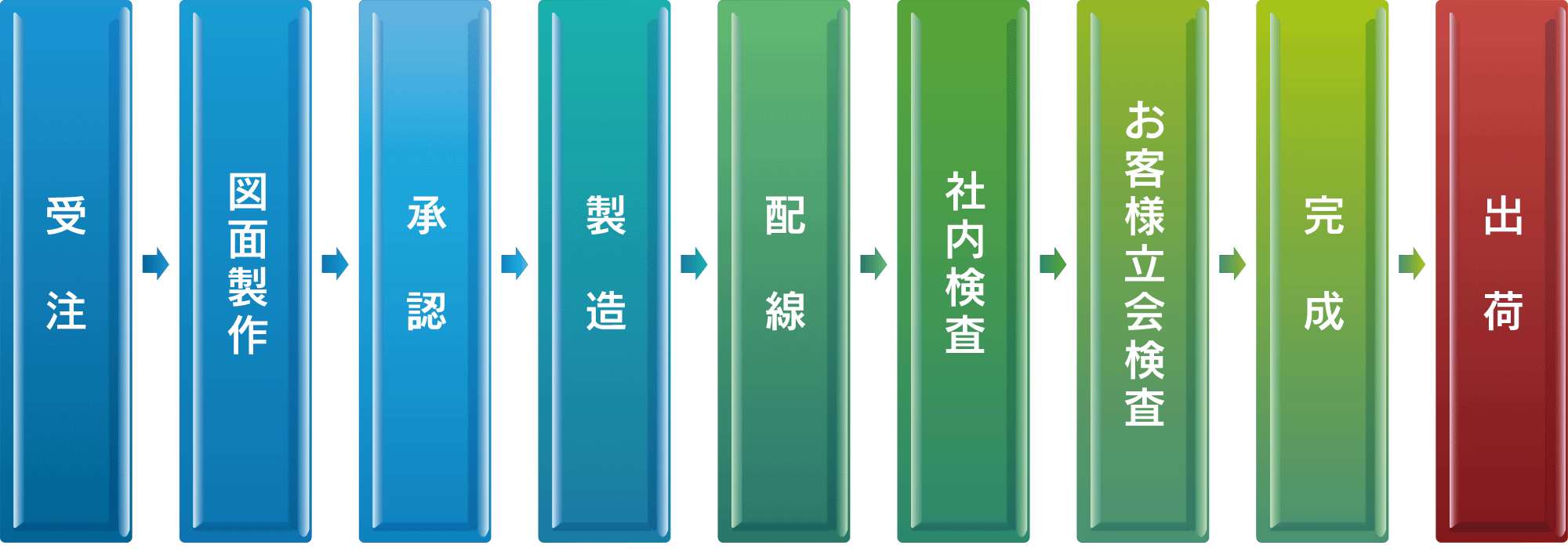
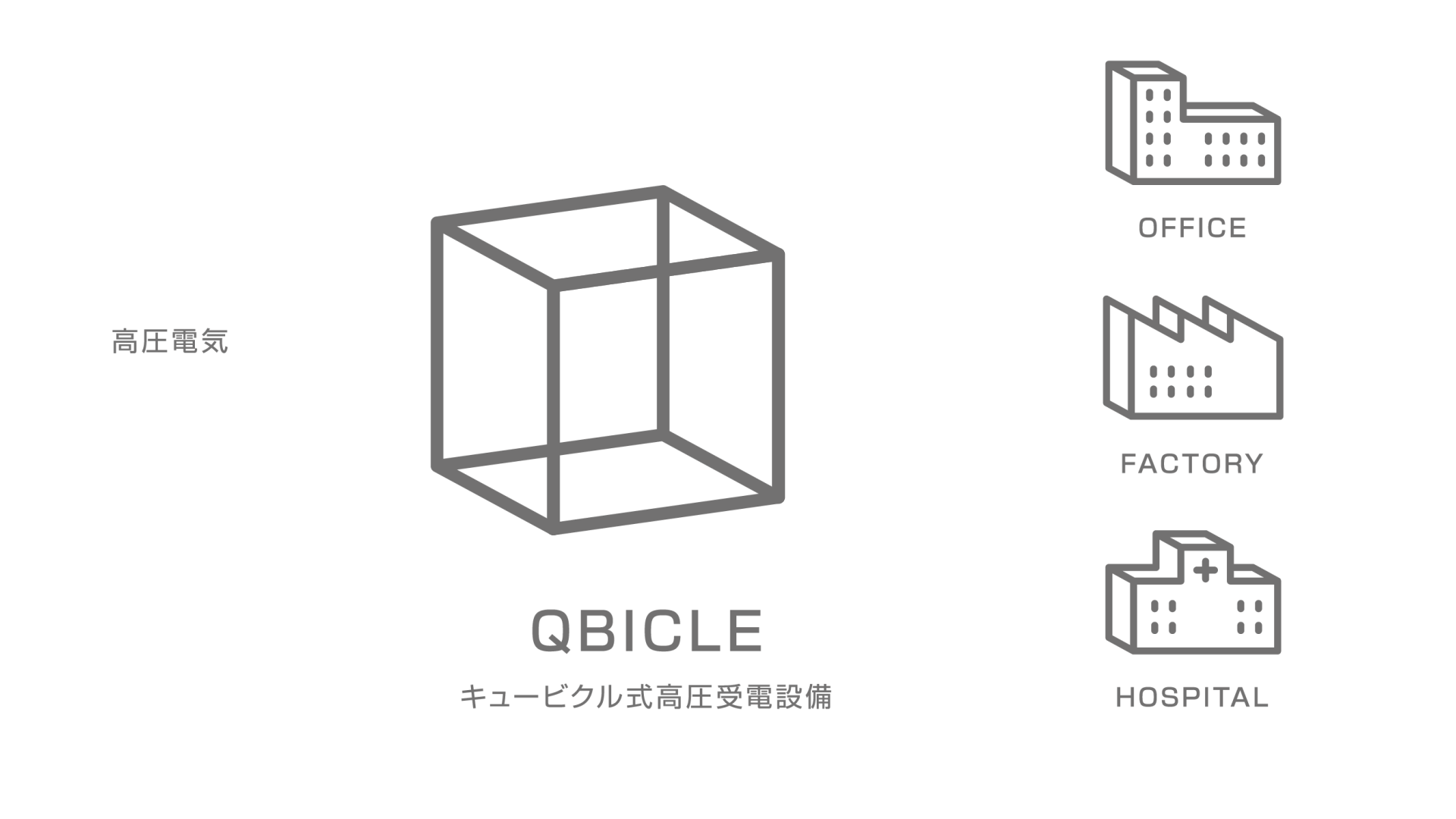
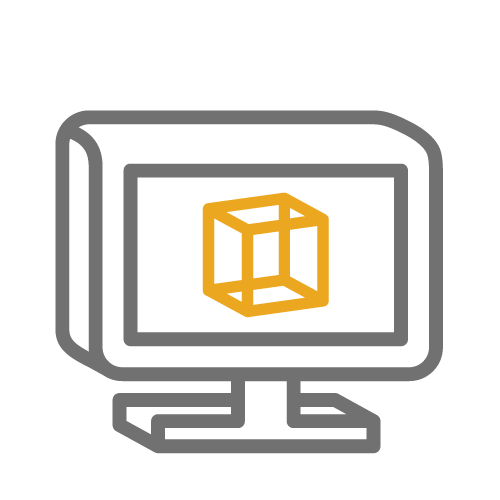
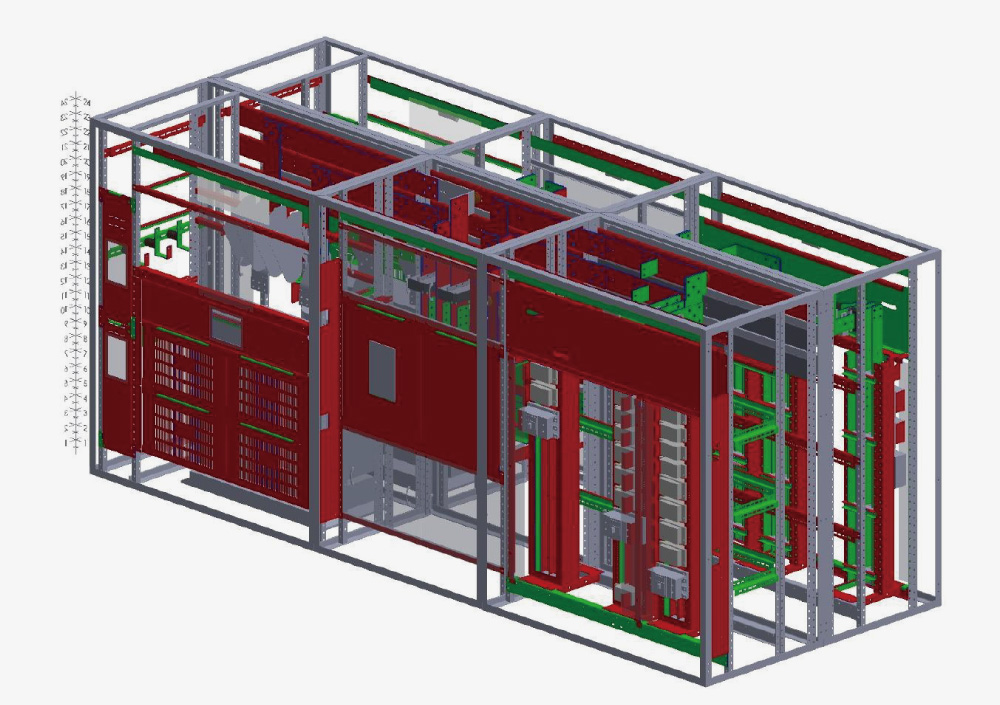
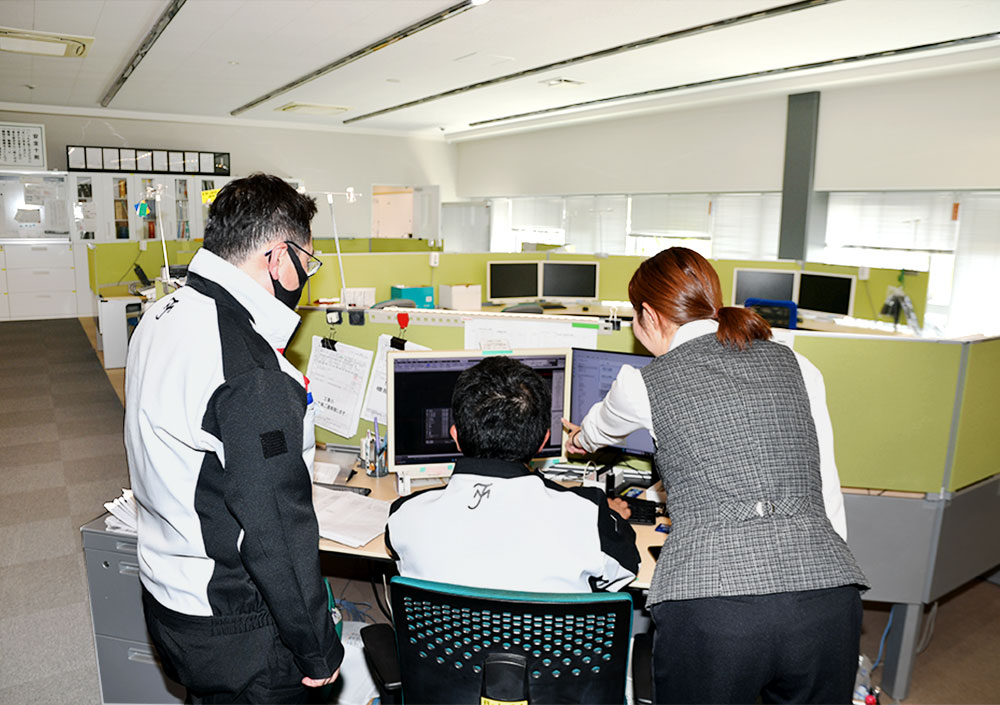
電気設計 (受変電設備の電気の流れ) 構造設計 (受変電設備の外観・金具・配置) : CADソフトを利用し、お客様の要望に合わせて、綿密に設計していきます。
(左図)3D CAD: 複雑な構造の案件は3DCADにて金具1つ1つから検証し製造を行います。
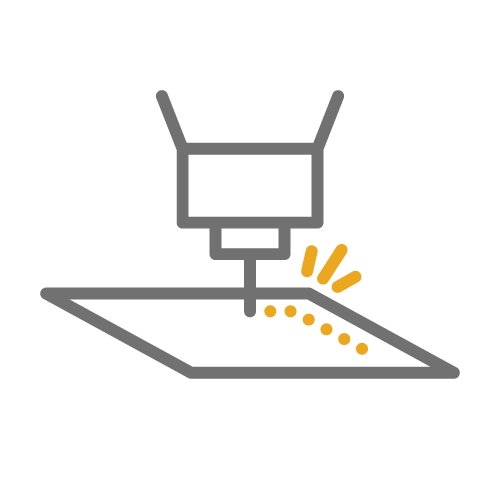
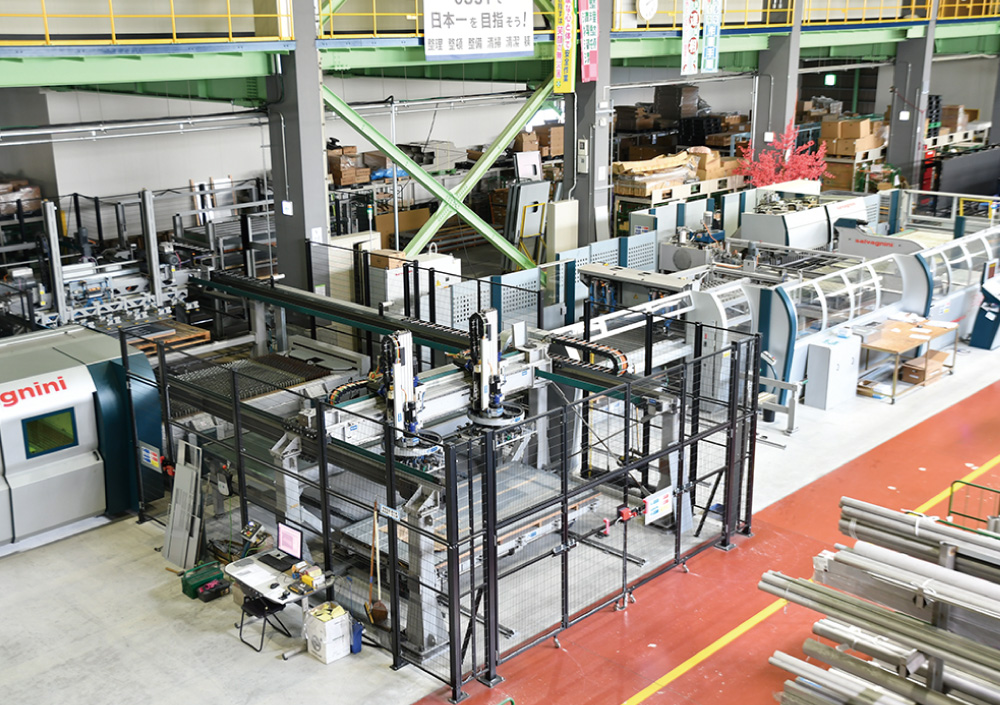
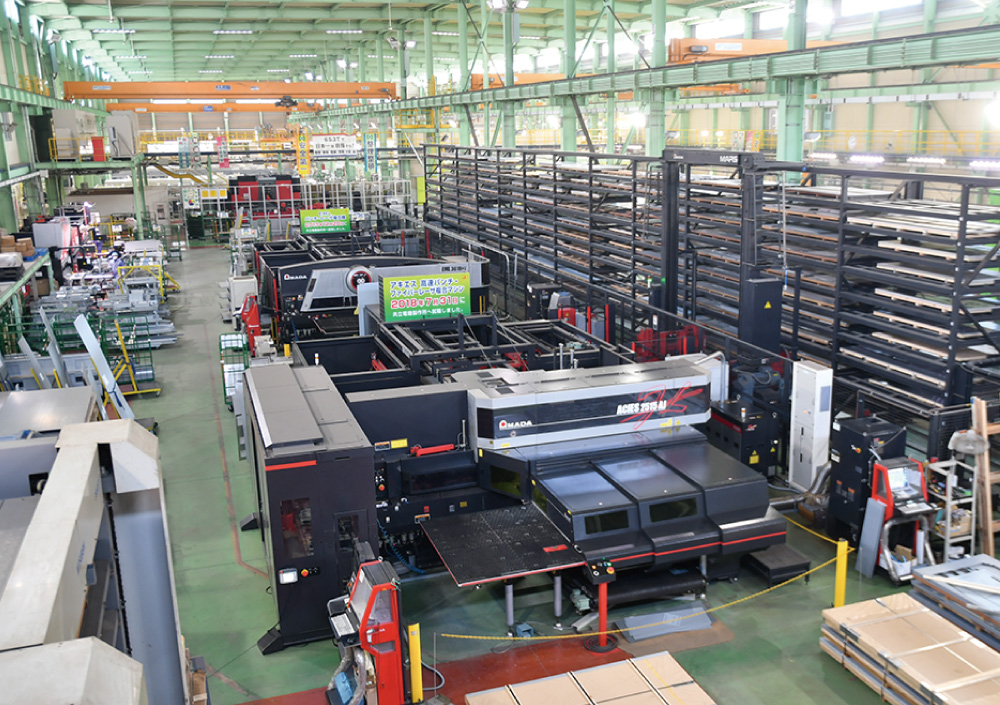
加工: 1枚の鉄板を加工(レーザー切断、穴あけ、パンチ)し、受変電設備(キュービクル)のパーツを準備していきます。大型装置を導入しており、24時間稼働体制を構築しています。

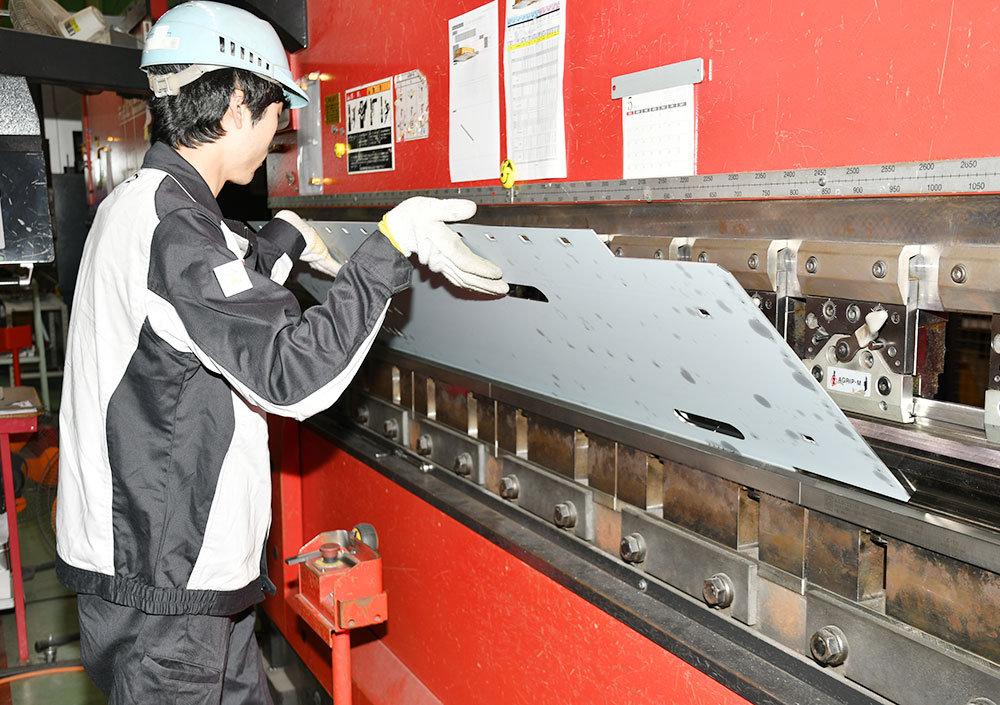
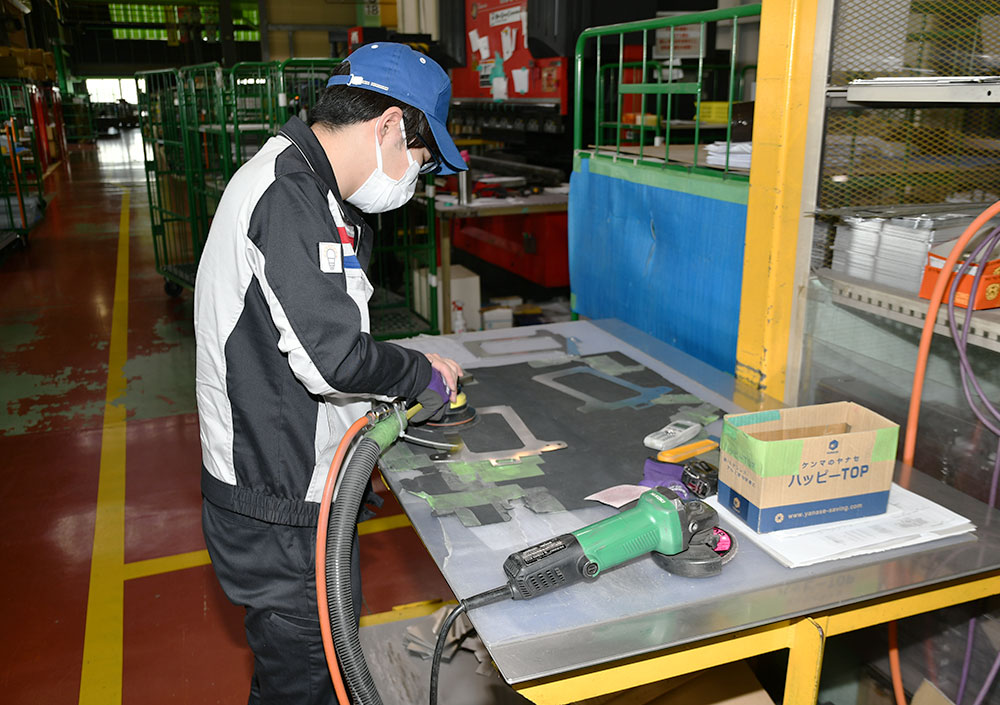
曲げ: 前工程で加工されたパーツを用途に合わせて、3D部品図のデータを利用し、機械(小さいオブジェクトは手作業)により曲げます。また、2メートルを超す大型のオブジェクトに関しては、腰への負担を減らす為、機械を導入しております。
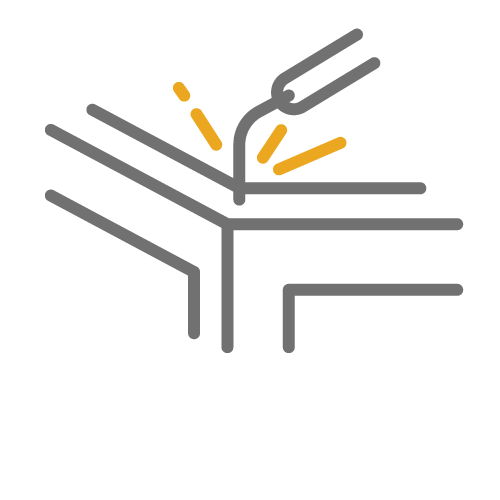
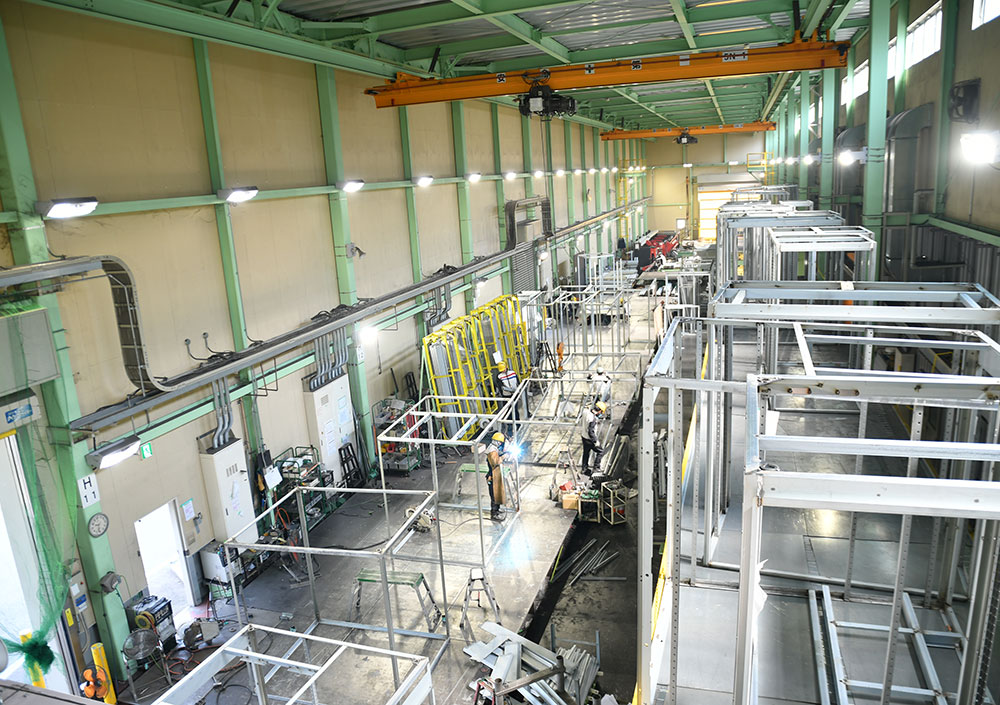
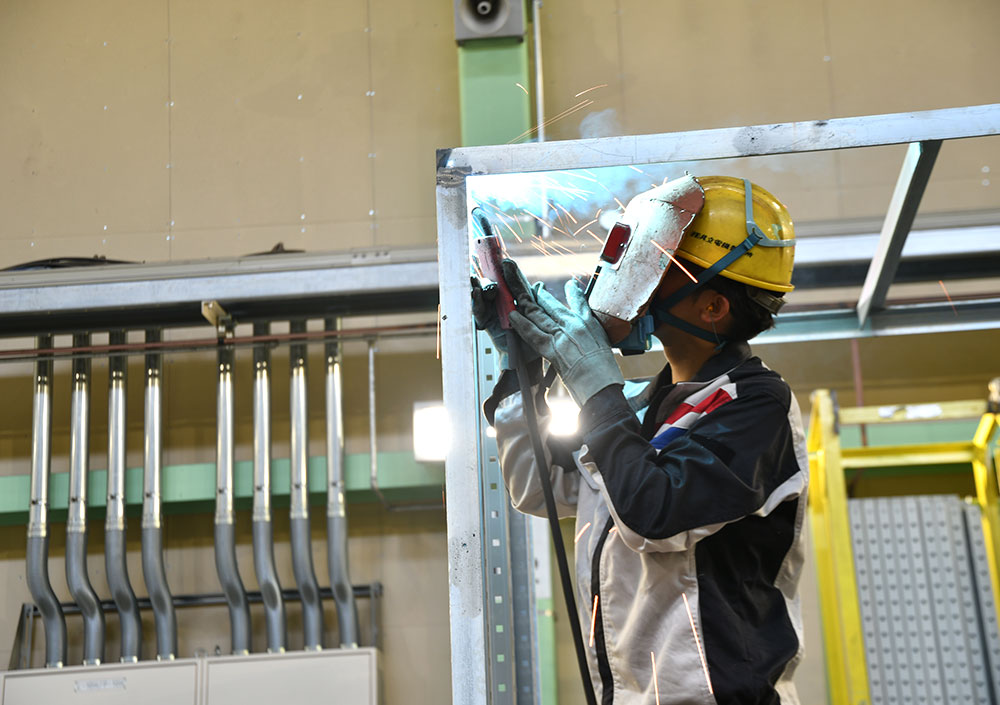
フレーム溶接: 屋内、屋外問わず全てのフレームは溶接加工にて製造しております。強度はもちろん、動力TR500KVAまで盤内に組込んだまま吊上げ、搬入が可能となります。(鋼材は全て電気メッキを使用)
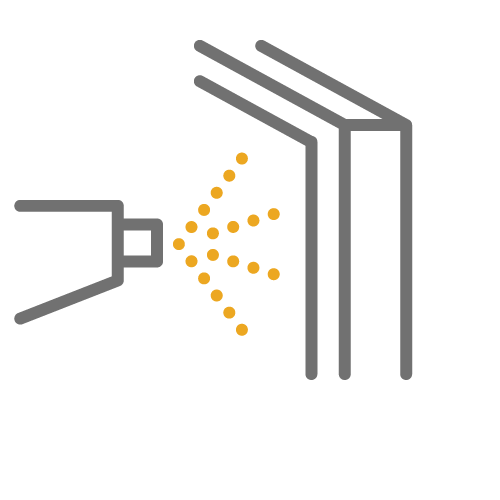
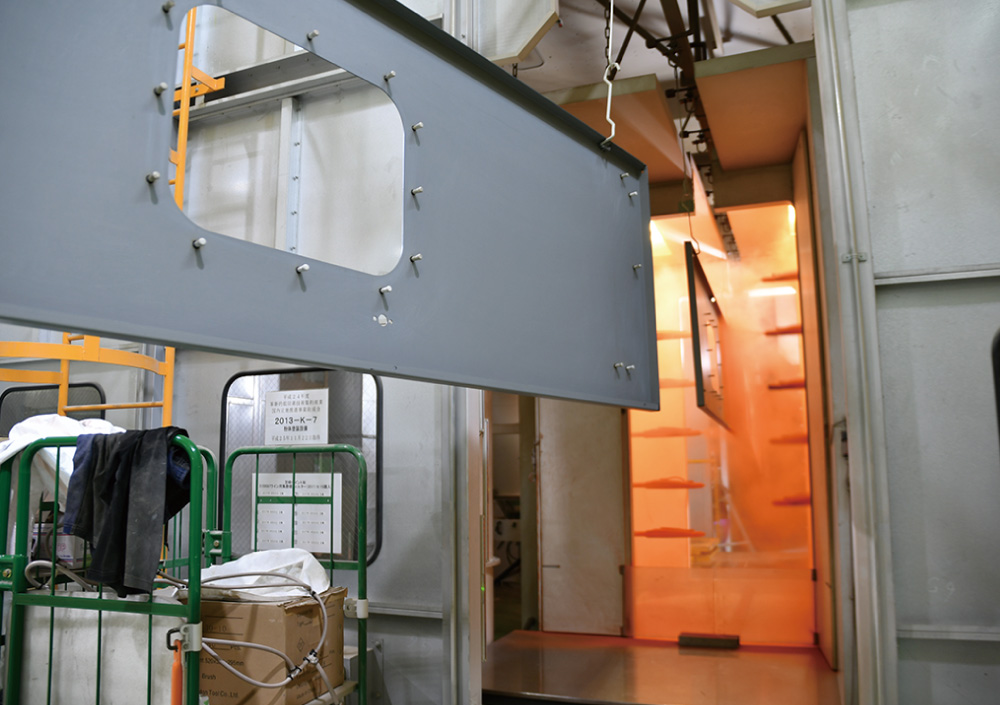
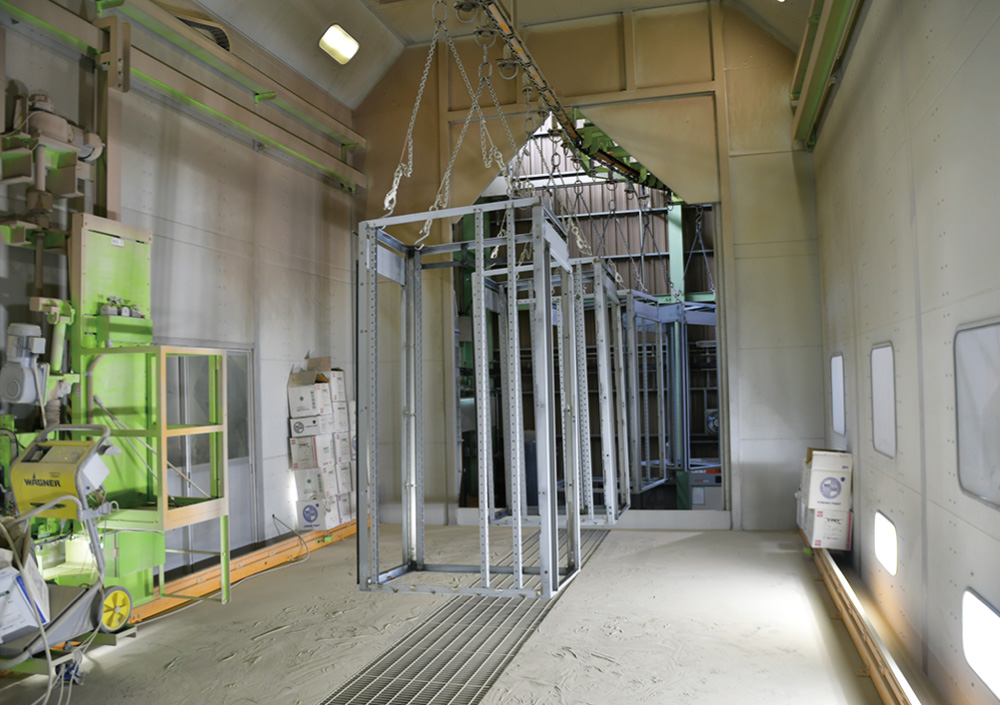
塗装: 塗装前処理設備(脱脂設備)・塗装設備(大型・小型)と焼き窯の3つのプラントで構成しています。粉体塗装ですので、お客様が要望する色の調合、全艶塗装/半艶塗装/重耐塩塗装と受変電設備を設置する環境に合わせて塗装していきます
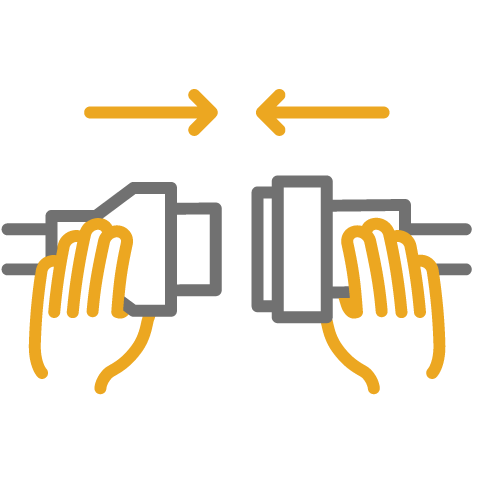
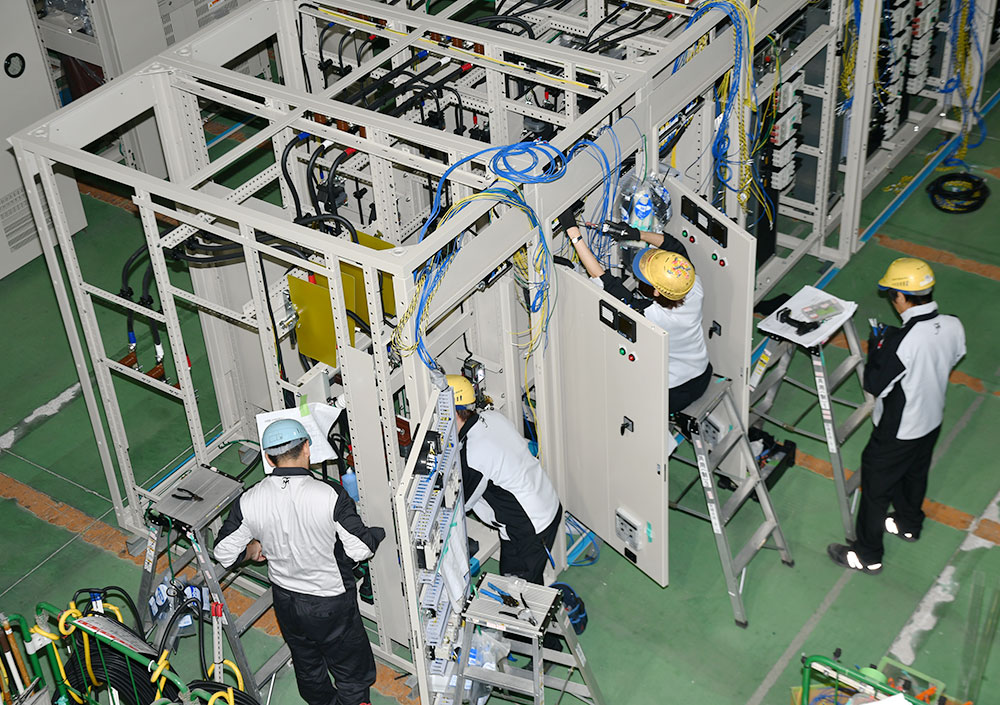
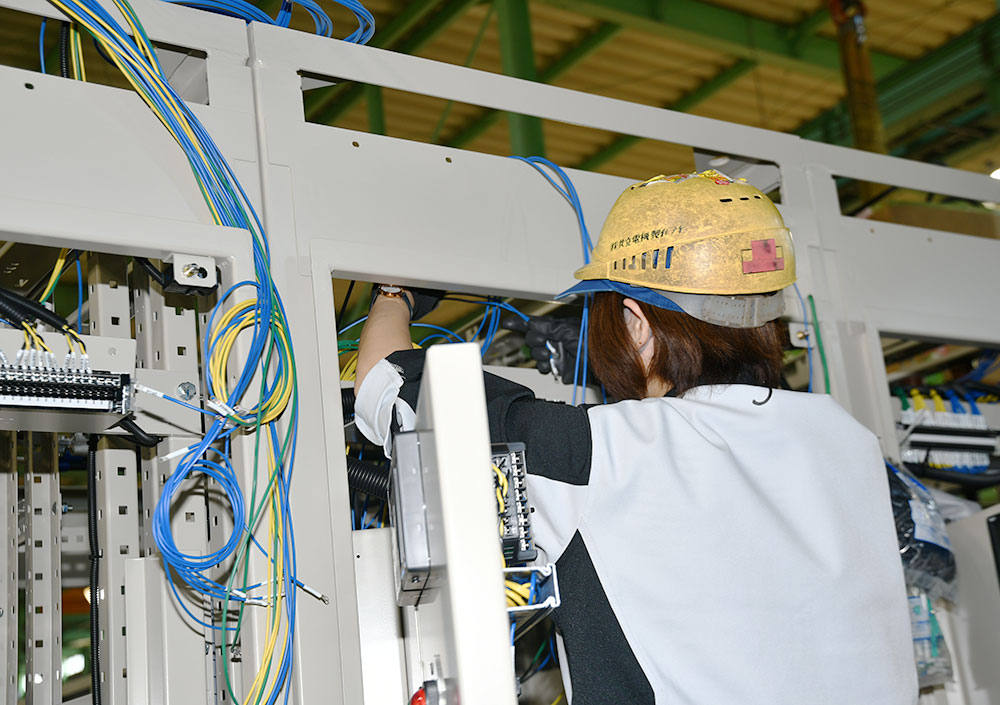
配線: 電気を通す為に、受変電設備を構成する機器をケーブルで配線をしていきます。主に、主回路・制御回路配線作業などがあります。
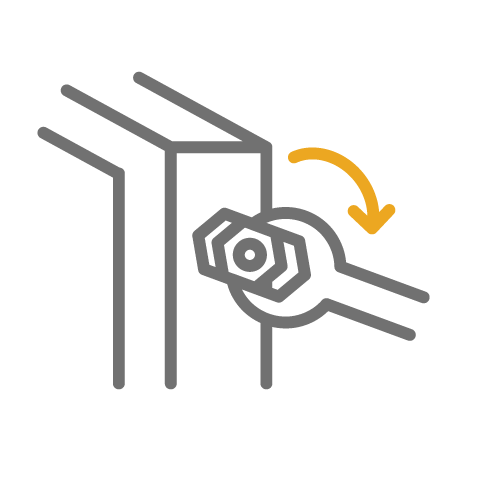
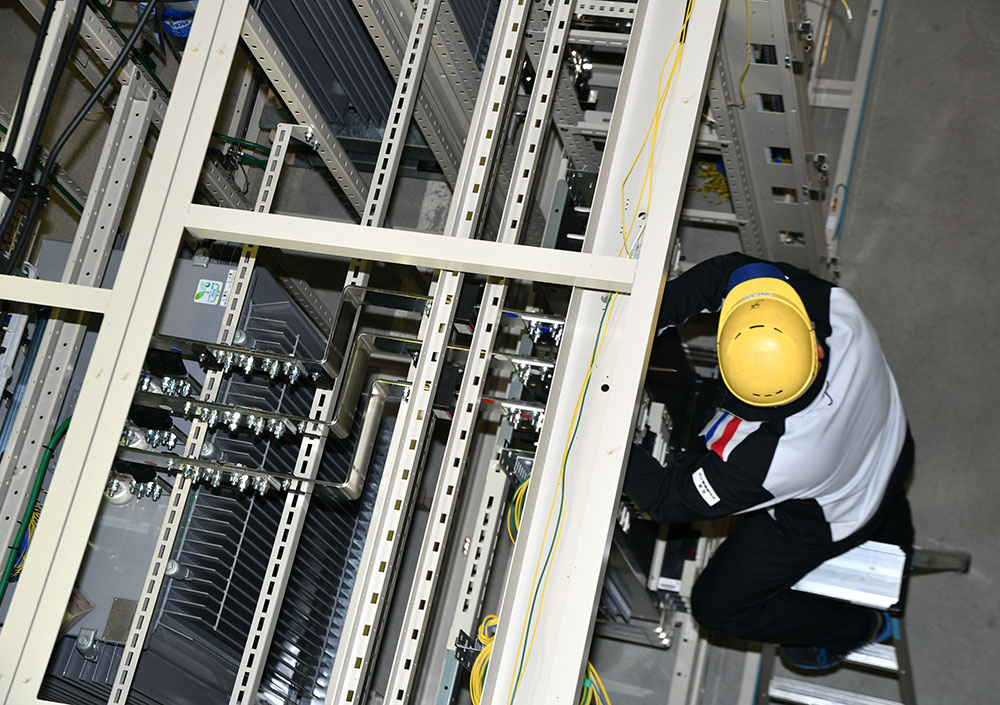
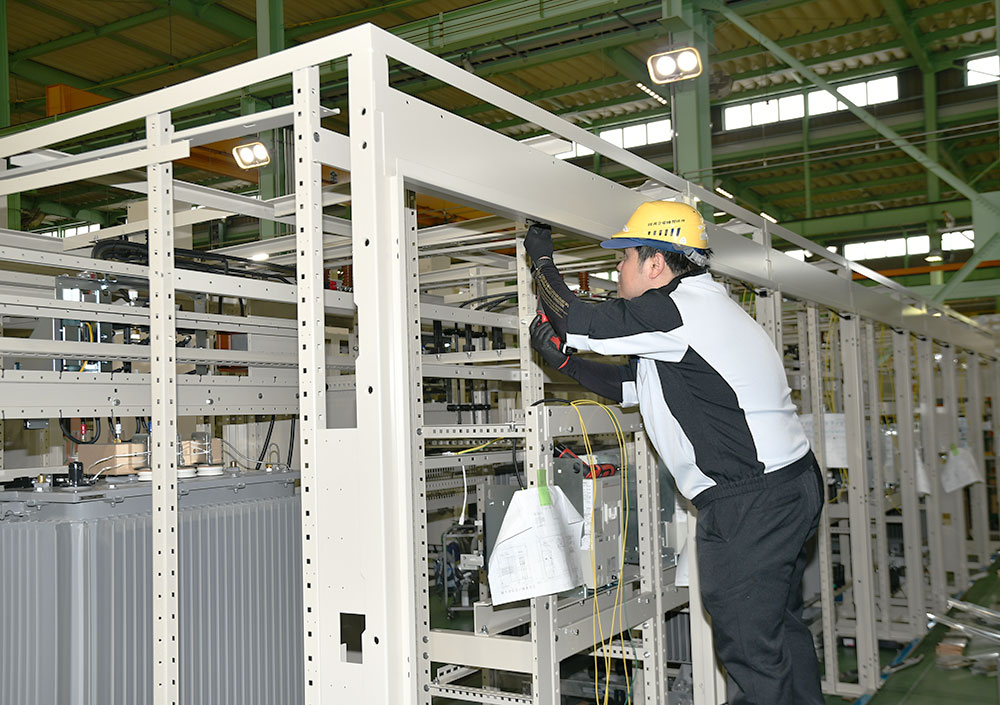
組立: 受変電設備を完成品にする為に、扉・屋根・銘板・オプションパーツなど組み立てていきます。
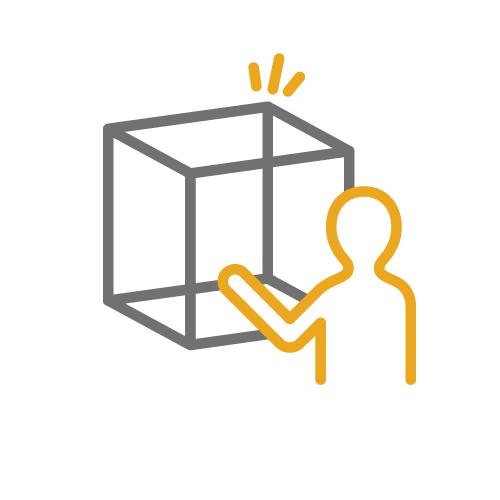
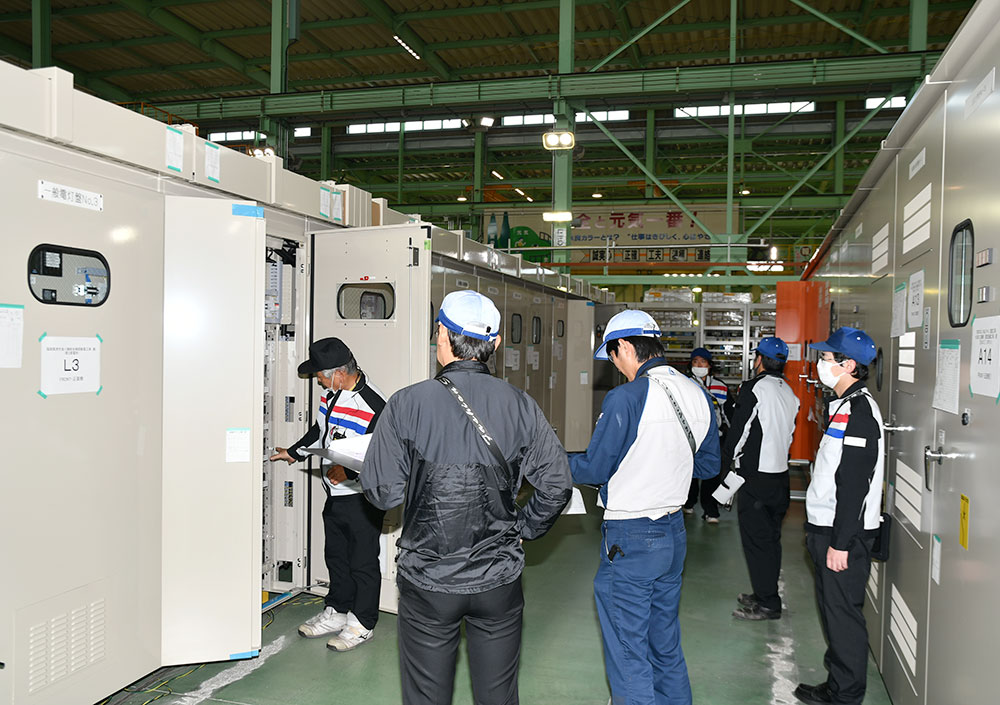
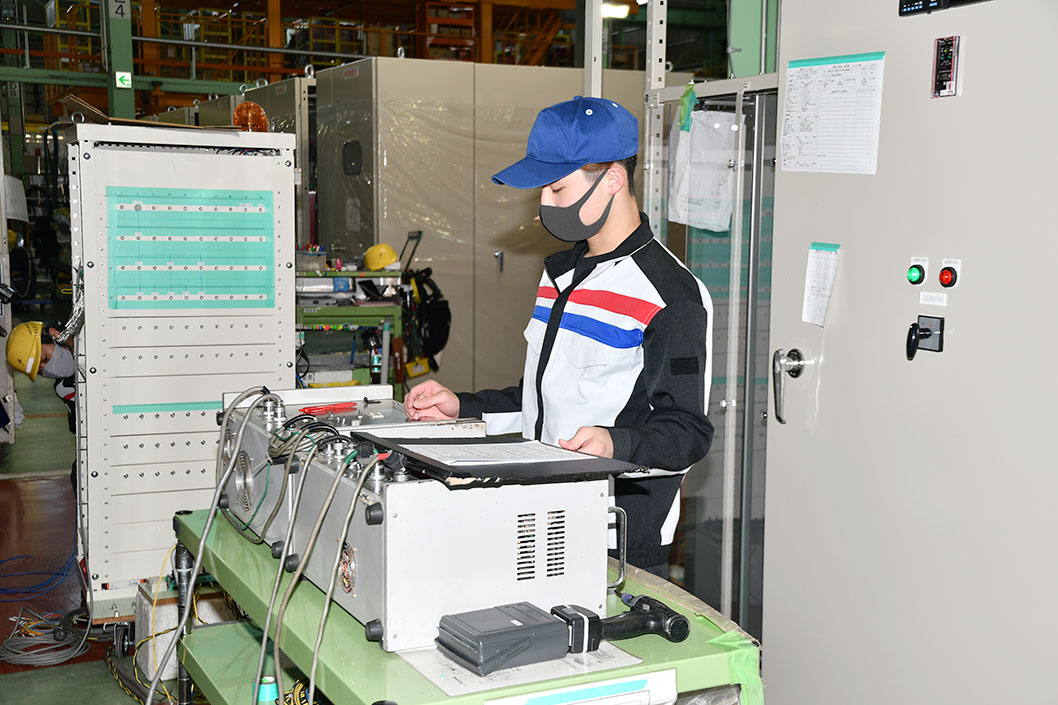
検査: 出荷前に製品不良が無いか、お客様(エンドユーザー)に対する製品品質の保証をする為に、外観検査・通電試験を実施しております。また、お客様に工場にお越し頂く立会検査も推奨しております。
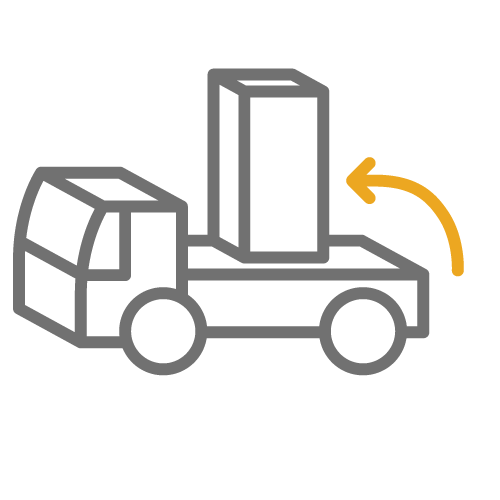
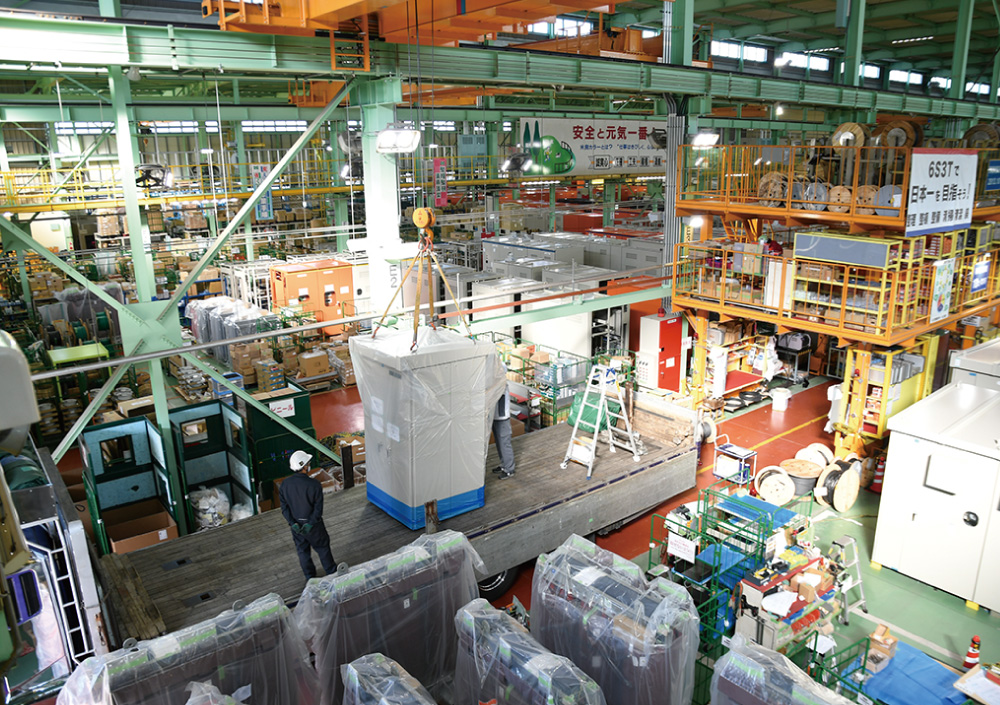
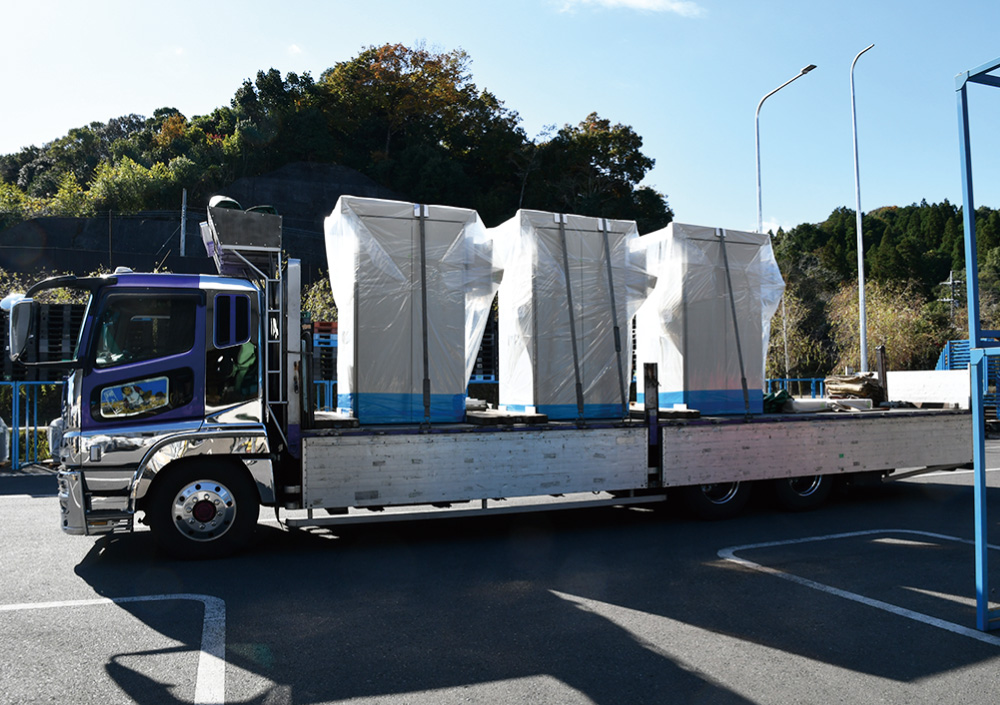
積込: Made in Miyazaki. 宮崎から日本全国各地へ安全・安心に商品をお届けいたします。